The Scientific Research Behind Porosity: A Comprehensive Guide for Welders and Fabricators
Recognizing the complex systems behind porosity in welding is critical for welders and producers striving for impeccable workmanship. From the composition of the base materials to the details of the welding process itself, a multitude of variables conspire to either exacerbate or alleviate the visibility of porosity.
Comprehending Porosity in Welding
FIRST SENTENCE:
Exam of porosity in welding exposes vital understandings right into the honesty and high quality of the weld joint. Porosity, identified by the presence of cavities or voids within the weld steel, is an usual concern in welding processes. These gaps, otherwise appropriately dealt with, can compromise the structural integrity and mechanical residential properties of the weld, causing possible failures in the ended up item.
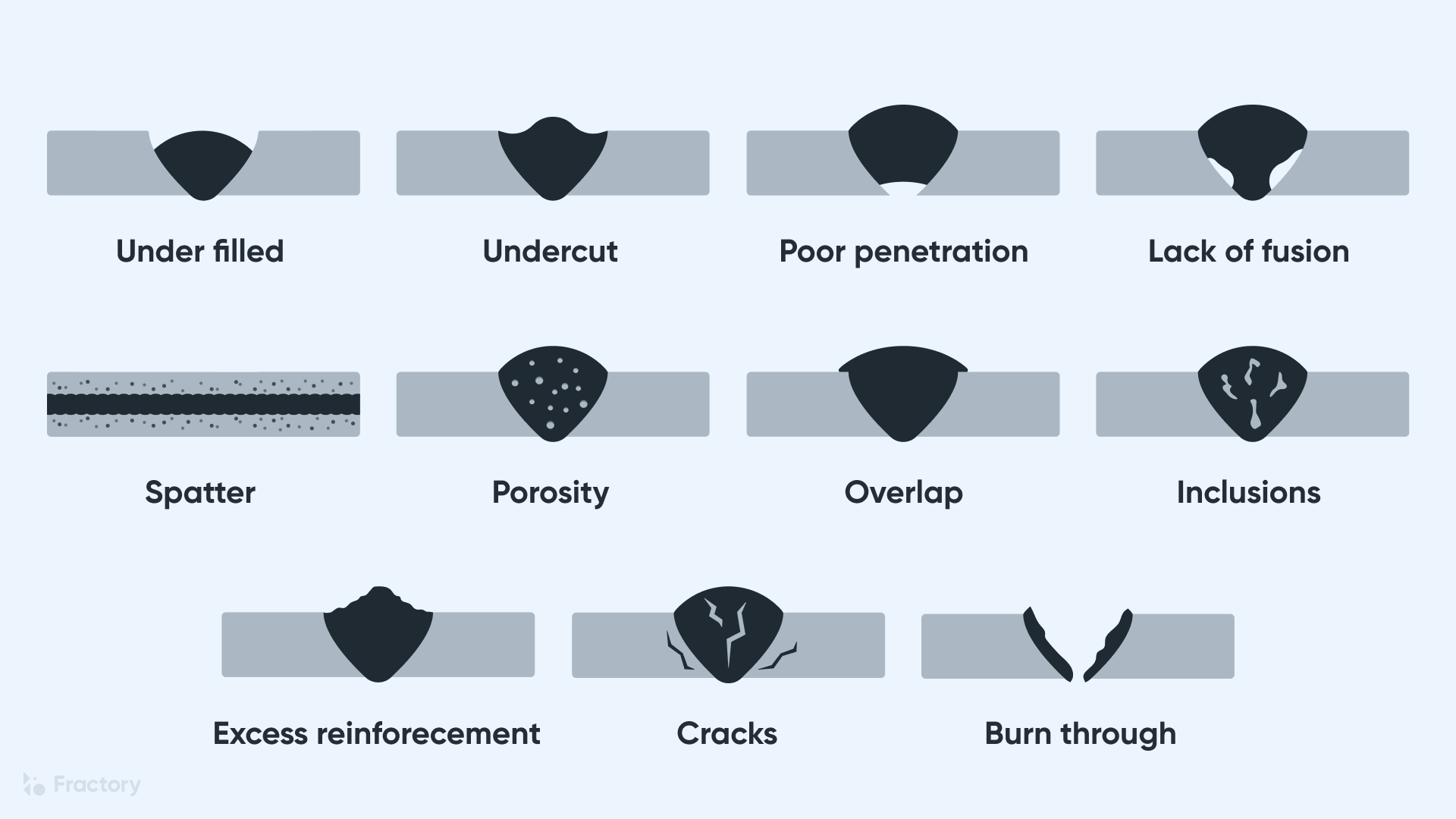
To spot and evaluate porosity, non-destructive screening methods such as ultrasonic testing or X-ray inspection are commonly utilized. These methods enable the identification of interior defects without endangering the stability of the weld. By examining the dimension, shape, and distribution of porosity within a weld, welders can make educated choices to improve their welding procedures and attain sounder weld joints.
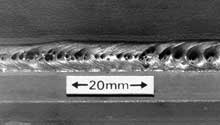
Aspects Affecting Porosity Development
The occurrence of porosity in welding is affected by a myriad of variables, varying from gas shielding performance to the details of welding criterion setups. Welding parameters, consisting of voltage, existing, take a trip speed, and electrode kind, additionally effect porosity development. The welding strategy utilized, such as gas steel arc welding (GMAW) or protected steel arc welding (SMAW), can affect porosity development due to variations in warmth distribution and gas coverage - What is Porosity.
Impacts of Porosity on Weld Quality
Porosity development dramatically endangers the architectural integrity and mechanical residential properties of bonded joints. When porosity is existing in a weld, it develops voids or cavities within the material, minimizing the general stamina of the joint. These spaces serve as stress and anxiety concentration points, making the weld more prone to splitting and failing under tons. The visibility of porosity also deteriorates the weld's resistance to deterioration, as the trapped air or gases within deep spaces can respond with the surrounding setting, leading to degradation gradually. In addition, porosity can impede the weld's capacity to hold up against stress or effect, further endangering the total high quality and reliability of the bonded framework. In critical applications such as aerospace, automobile, or structural buildings, where security and sturdiness are paramount, the harmful results of porosity on weld top quality can have extreme repercussions, emphasizing the value of reducing porosity via proper welding strategies and treatments.
Techniques to Reduce Porosity
To boost the quality of welded joints and guarantee architectural honesty, welders and producers use details strategies intended at reducing the development of voids and dental caries within the material throughout the welding procedure. One effective approach to decrease porosity is to ensure proper material preparation. This includes detailed cleansing of the base metal to eliminate any kind of contaminants such as oil, grease, or moisture that could add to porosity development. Additionally, utilizing the proper welding parameters, such as the correct voltage, current, and travel rate, is essential in preventing porosity. Keeping a consistent arc size and angle throughout welding also helps decrease the likelihood of porosity.

Using the appropriate welding technique, such as back-stepping or employing a weaving movement, can likewise assist disperse warmth equally and reduce the opportunities of porosity formation. By executing these strategies, welders can efficiently decrease porosity and create top notch welded joints.
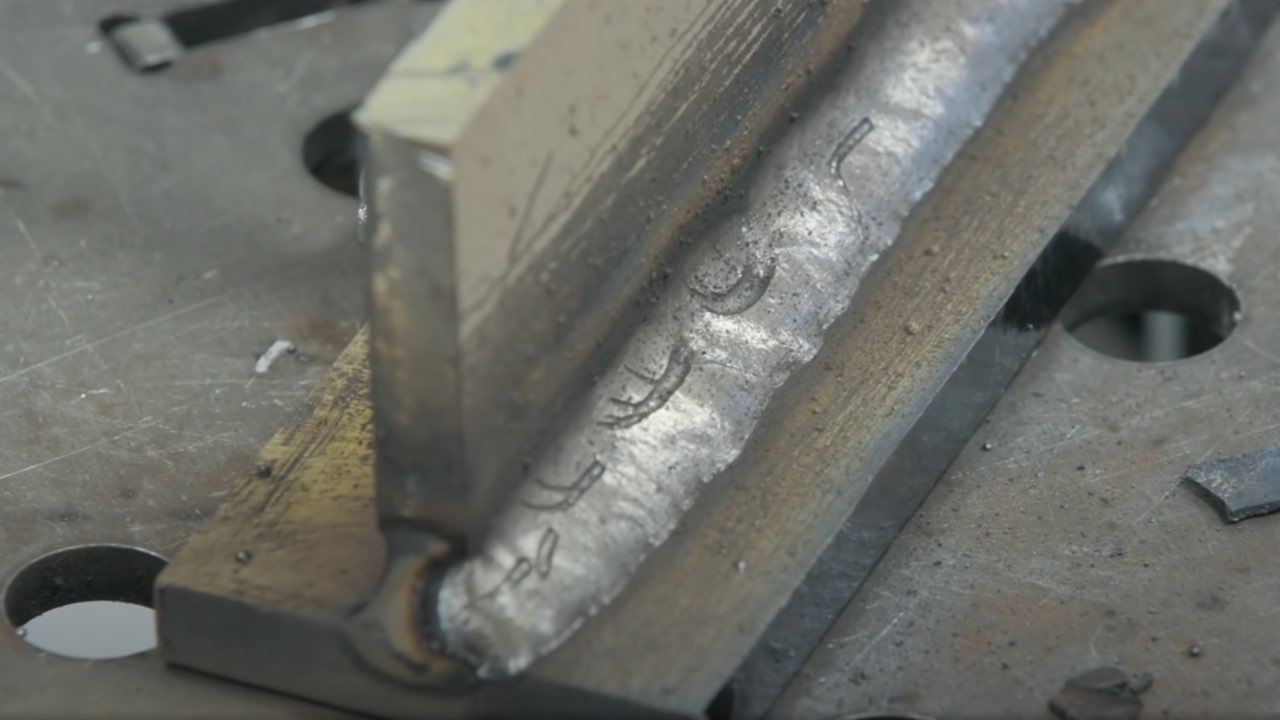
Advanced Solutions for Porosity Control
Carrying out innovative modern technologies and ingenious techniques plays an essential duty in accomplishing superior control over porosity in welding procedures. One innovative solution is making use of advanced gas mixes. Shielding gases like helium or a combination of argon pop over to this web-site and hydrogen can assist decrease porosity by supplying much better arc security and boosted gas coverage. In this page addition, employing sophisticated welding techniques such as pulsed MIG welding or changed atmosphere welding can likewise assist alleviate porosity problems.
One more advanced solution involves using advanced welding equipment. Utilizing tools with built-in attributes like waveform control and advanced power resources can enhance weld top quality and minimize porosity dangers. The execution of automated welding systems with accurate control over parameters can considerably decrease porosity flaws.
Furthermore, including innovative monitoring and assessment modern technologies such as real-time X-ray imaging or automated ultrasonic screening can assist in discovering porosity early in the welding procedure, enabling for prompt restorative actions. Generally, incorporating these innovative options can greatly enhance porosity control and boost the total high quality of bonded parts.
Final Thought
In verdict, comprehending the scientific research behind porosity in welding is vital for welders and producers to generate premium welds - What is Porosity. Advanced options for porosity control can even more boost the welding procedure and click here for info ensure a strong and reliable weld.
Comments on “What is Porosity in Welding: Recognizing Its Reasons and Enhancing Your Abilities”